Building a Greener Future: Sustainable Concrete Production with Volumetric Mixers
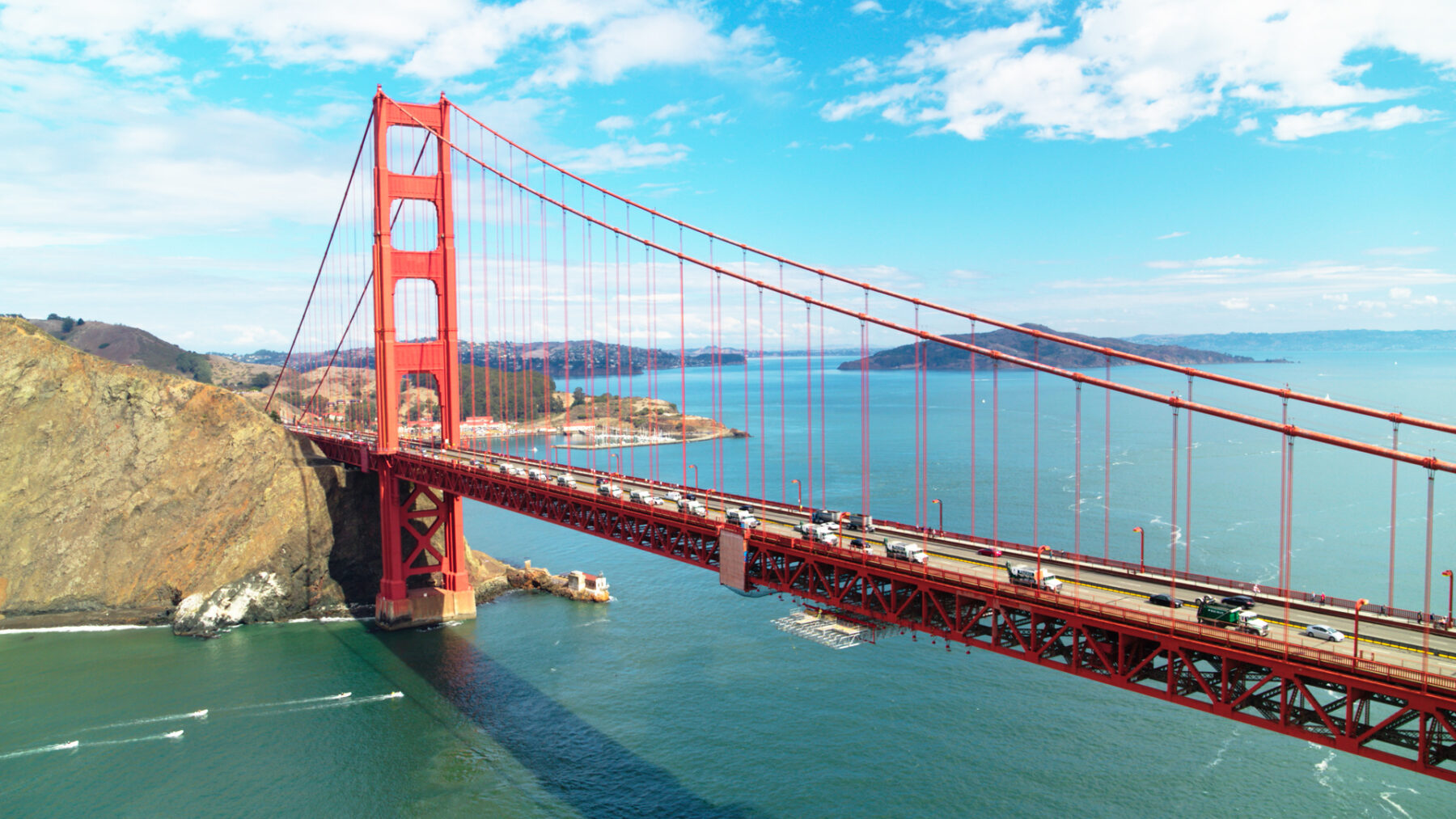
In an era of increasing environmental awareness, the construction industry is actively seeking more sustainable practices. One key area under scrutiny is concrete, a widely used material. Forward-thinking contractors are increasingly turning to innovative solutions like volumetric concrete mixers to reduce their environmental footprint and enhance sustainability in concrete production.
The Growing Demand for Sustainable Construction
Across the globe, green building regulations and standards are evolving, but the commitment to sustainable change is a universal one. From the initial design phase to demolition, nearly every aspect of the construction industry is being evaluated for its environmental impact. This includes concrete, a fundamental material. Consequently, a growing number of contractors are adopting volumetric mixers to actively reduce waste and lower carbon emissions, while also maintaining cost control.
Leading the Way in Sustainable Concrete Practices
Mike Bauman, president and co-founder of Bauman Landscape and Construction, has been a strong advocate for volumetric concrete mixers. He has strategically leveraged each technological advancement in this field to expand his business and meet the growing demands for sustainable construction.
“When you partner with larger general contractors and aim for LEED credits on projects, it significantly enhances your appeal to them,” explains Bauman. “They actively seek out partners who can help them achieve these credits and present a more environmentally conscious image to their clients.”
Today, Bauman’s company operates a fleet of 18 Cemen Tech C60 volumetric concrete mixers. These mixers have played a crucial role in building some of San Francisco’s most iconic and complex structures, including the Palace of Fine Arts, Golden Gate Park Carousel, Lafayette Park, and Jefferson Street in Fisherman’s Wharf.
“The city is very supportive of our volumetric mixers. They prefer the mix quality compared to traditional barrel mixers,” says Bauman. “We’ve had numerous inquiries from competitors who have seen our mixers in action, leading to new business opportunities.”
By Mark Rinehart
With over two decades of experience, Mark Rinehart, Vice President of Sales and Marketing for Cemen Tech, has guided construction businesses through technological advancements, helping them improve their operations and embrace sustainable solutions. Mark leads the strategy and execution of sales and marketing initiatives at Cemen Tech, the global leader in the volumetric concrete mixer industry. His focus on driving sales, exploring growth opportunities, and managing client relationships has been instrumental to the company’s success.
Sustainable Concrete Solutions with Bauman Landscape
Bauman Landscape & Construction switched to Cemen Tech C60 mixers to improve concrete supply, save costs, and meet sustainability goals with 100% recycled aggregate.
Reduced Waste Through Precise Material Management
Minimizing the environmental impact of construction starts with making informed material choices and ensuring accuracy. Volumetric concrete trucks excel in both areas. These innovative mobile concrete mixers store each ingredient – sand, stone, cement powder, supplementary cementing materials, water, and additives – in separate compartments. When it’s time to pour, the contractor simply selects the desired mix design, and within a mere 15 seconds, fresh concrete is ready.
While the National Ready Mixed Concrete Association estimates that approximately 5% to 10% of traditional ready-mix concrete deliveries are returned to the plant due to overages or quality issues, volumetric mixers offer a more precise approach. Innovations like the dual auger cement metering system in Cemen Tech C60 Series mixers ensure consistent mix designs with a remarkable accuracy of plus or minus 1% on every pour.
This volumetric technology provides contractors with greater flexibility to produce their own concrete, thereby conserving valuable raw materials and significantly reducing the environmental impact of disposal. The U.S. Environmental Protection Agency estimates that construction and demolition waste totals up to 600 million tons annually, with concrete and asphalt concrete comprising approximately 85% of this figure. Volumetric mixers empower contractors to produce only the exact amount of concrete needed – no more, no less, thus minimizing waste.
Bauman Landscape and Construction was an early adopter of using 100% recycled aggregate in their concrete mixes. They blend stone with approximately 50% concrete dust and virgin sand, resulting in a mix that is 75% recycled material. “When you undertake a project for the city, you are required to submit monthly reports detailing your recycling efforts – how you’ve handled all waste materials and how it has been utilized. Failure to submit these reports can result in non-payment,” explains Bauman.
Water Conservation: A Key Aspect of Sustainability
Water conservation is particularly critical in regions with limited water resources. According to the CSA Group standards organization, traditional barrel trucks typically require around 200 gallons of water for washout. In stark contrast, volumetric mixers utilize only a mere eight to 10 gallons for the same purpose, demonstrating a significant reduction in water usage.
Lower Emissions Through Reduced Travel
Volumetric technology also allows contractors to produce concrete with varying strengths (PSI) from the same unit without leaving the job site. This significantly reduces the number of truck trips, keeping trucks off the road and eliminating the challenges associated with “hot loads” (concrete that begins to set before being poured). Fewer loads translate directly to lower vehicle emissions and reduced fuel costs. In fact, two volumetric trucks on a job site can potentially pour as much concrete in a single day as 100 drum mixers.
Furthermore, hundreds of different mix designs can be pre-programmed into the onboard computer of a volumetric mixer. This enables the operator to select and initiate the process with the touch of a button, ensuring fresh concrete every time without the need to switch equipment.
For the Bauman Landscape and Construction team, this translates to fewer loads and quicker project completion times. “We handle a lot of streetscape projects, and the curb, gutter, and sidewalks often require different concrete mixes,” notes lead project manager Angela Bauman. “We used to need three separate short loads just to pour a curb ramp.” With Cemen Tech C60 volumetric concrete mixers, the mix design can be adjusted for each specific portion of the project and poured from a single truck.
For instance, in San Francisco, handicap ramps are required to be a dark, contrasting color, while bus lanes are a bright red. When Bauman’s team pours both the ramp and the adjacent sidewalk or two different street lanes, they can mix the precise amount of each color needed directly on-site, eliminating the need to order multiple separate concrete loads with different colors from a ready-mix plant.
For Mike Bauman, this flexibility has revolutionized their ability to move between or within the same job with unprecedented ease. “We’ve equipped our Cemen Tech C60s with liquid color systems, which is fantastic because almost everything we do involves color. Even simple sidewalks often have color in them,” he explains. “We probably have around 25 different mix designs pre-loaded to accommodate the diverse range of work we undertake.”
"*" indicates required fields
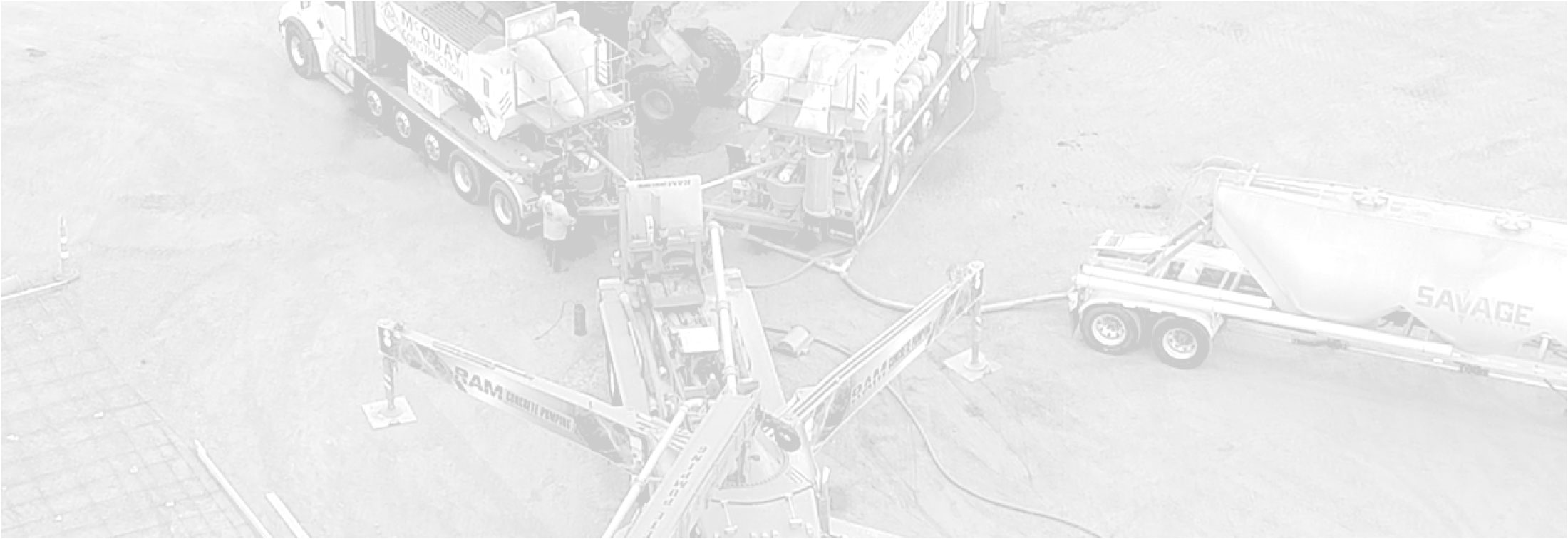