Volumetric Concrete Mixers for Large-Scale Residential Paving
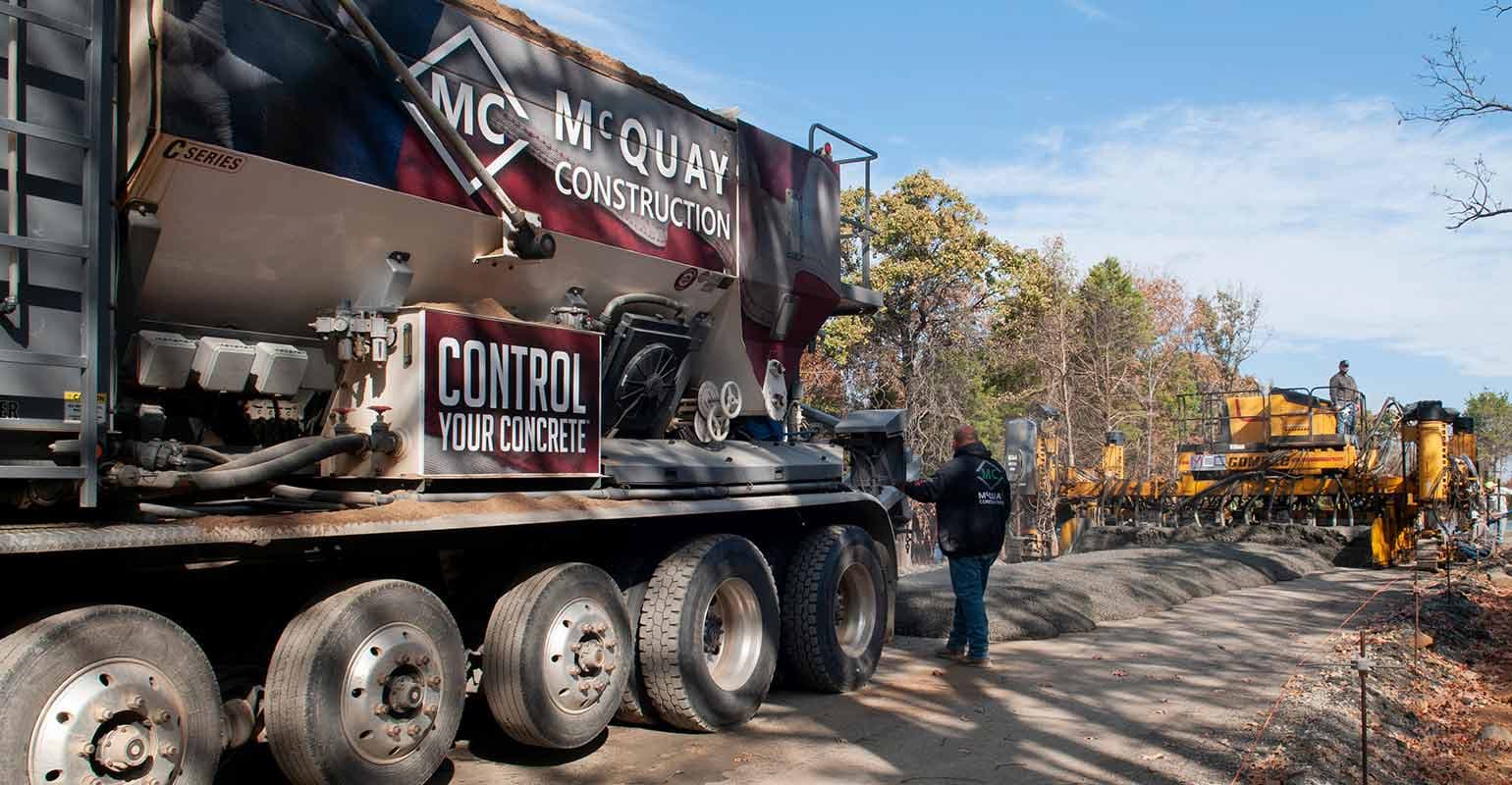
Finding an Efficient Concrete Solution
Zach McQuay Concrete faced a tough decision on how to efficiently supply concrete to a large-scale residential
project. The challenge was to find a method that would minimize costs and keep the project on schedule, especially with no nearby asphalt plants available.
The new residential development covering 700 acres included around 265 home sites and eight miles of roads. McQuay’s scope of work extended beyond concrete paving to cover utilities, water and electric lines, and tree removal. Given the complexity and scale, they required a solution that would allow them to manage all these elements efficiently on-site.
Choosing Volumetric Mixers for On-Site Control
With no asphalt plant nearby, asphalt became a less feasible option for McQuay.
“Asphalt here is tough, because there’s not an asphalt plant very close to us,” said McQuay. “With our volumetric trucks, we were able to make a mobile yard here, essentially, so we can do a high production right here on the grounds.
Transporting materials for asphalt paving would have caused significant delays and cost overruns. McQuay considered using traditional ready-mix trucks but was concerned about the consistency of the concrete and the potential for stop-and-start issues during the paving process.
How Volumetric Mixers Streamlined the Paving Process
McQuay decided to use volumetric mixers, which gave them the ability to create a mobile concrete yard directly at the job site. By eliminating the need to transport materials from distant plants, they gained greater control over the production and quality of their concrete. Three volumetric mixers were used on-site, ensuring that there was always concrete ready for the paver, thus avoiding downtime.
The volumetric mixers allowed McQuay to run continuous paving operations, producing around 350 yards of concrete a day and achieving 1,000 yards over two days each week. The mixers ensured that the concrete mix was consistent and the paver did not need to stop, which resulted in a smoother finish and fewer joints.
“Because the paver never stops. Our mud is very, very consistent. You’re able to stockpile 30, 40 feet in front of him, so the paver never has to stop,” said McQuay.
Leveraging ACCU-POUR™ for Material Management
McQuay used ACCU-POUR™ software to track materials and yields throughout the project. The technology allowed them to monitor the mix design closely, ensuring accuracy and preventing waste. This level of control provided peace of mind that each batch of concrete met the required standards.
The Benefits of Consistency and Fiber Reinforcement
The biggest advantage was the consistency of the concrete mix, which was crucial for the paving machine to operate without interruption. The finishers also appreciated the mix’s workability, which made their job easier and resulted in better finished roads. McQuay used fiber reinforcement in the concrete instead of rebar, which reduced setup time and kept the trucks moving efficiently without the need for extra equipment.
Success with Volumetric Mixers on Large Projects
McQuay’s decision to switch to volumetric mixers for this large-scale paving project resulted in a more efficient, cost-effective, and high-quality paving operation. The adaptability of volumetric mixers, combined with ACCU-POUR™ technology, allowed McQuay to control their concrete production on-site, making their operations smoother and more cost effective. This success highlights the advantages of volumetric mixers for general contractors looking to maintain control over their concrete operations while ensuring quality and cost savings.
Paving Success with Volumetric Mixers
McQuay Construction used volumetric mixers to handle large paving projects on-site, keeping the work moving smoothly and delivering consistent results.
Concrete Paving With A Volumetric Mixer
Because the paver never stops. Our mud is very, very consistent. You’re able to stockpile 30, 40 feet in front of him, so the paver never has to stop.
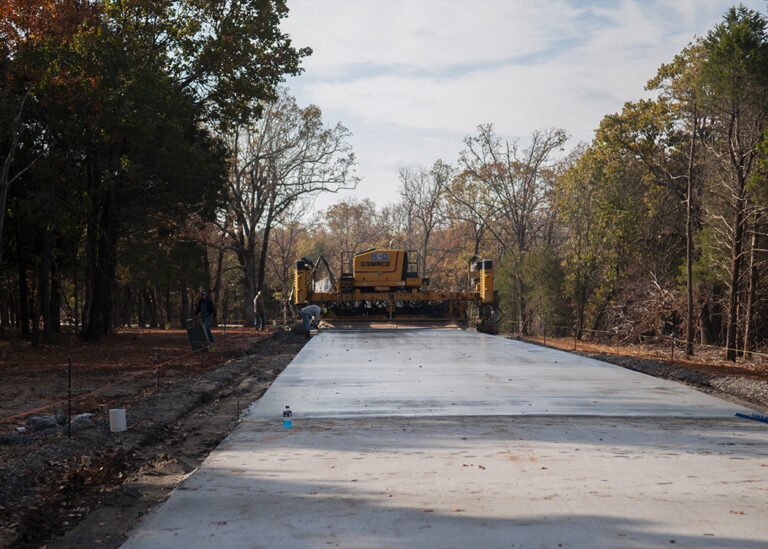
Cost Savings
The use of volumetric mixers brought concrete production costs close to the price of asphalt, eliminating the need for outsourcing.
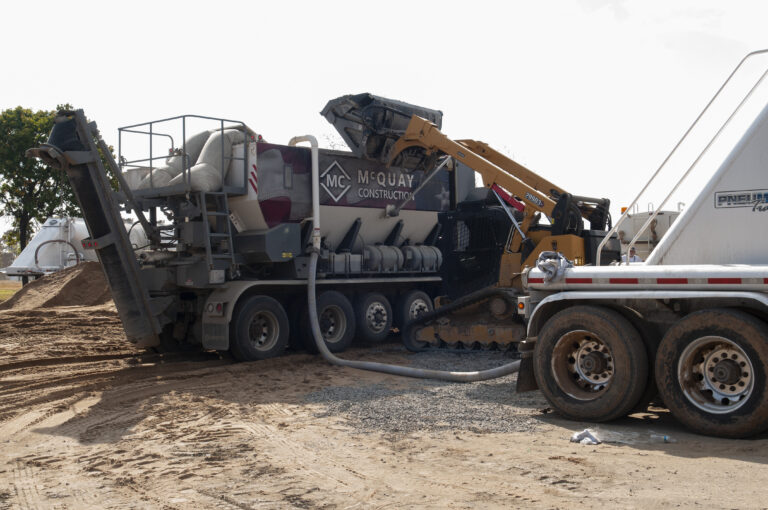
Productivity
The team could pour up to 1,000 yards of concrete over two days a week, maintaining continuous operations with three mixers
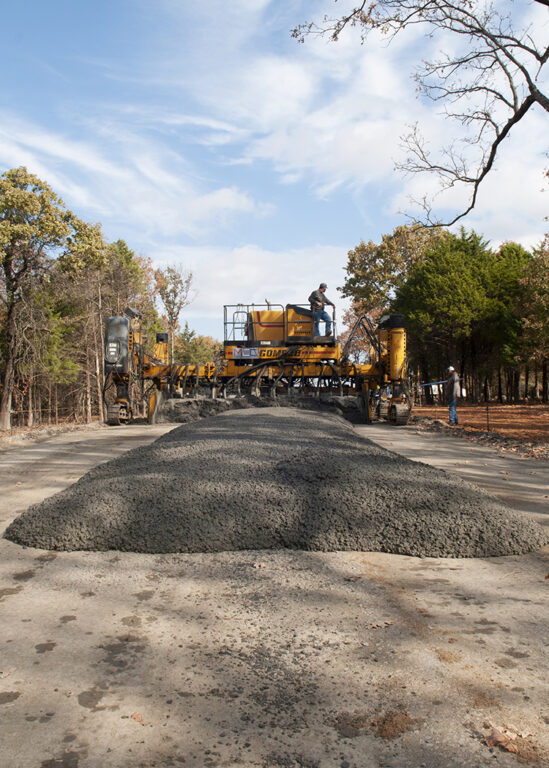
Consistency
The mixers ensured the concrete was uniform throughout the project, reducing the need for stop-and-start paving and creating smoother finishes.
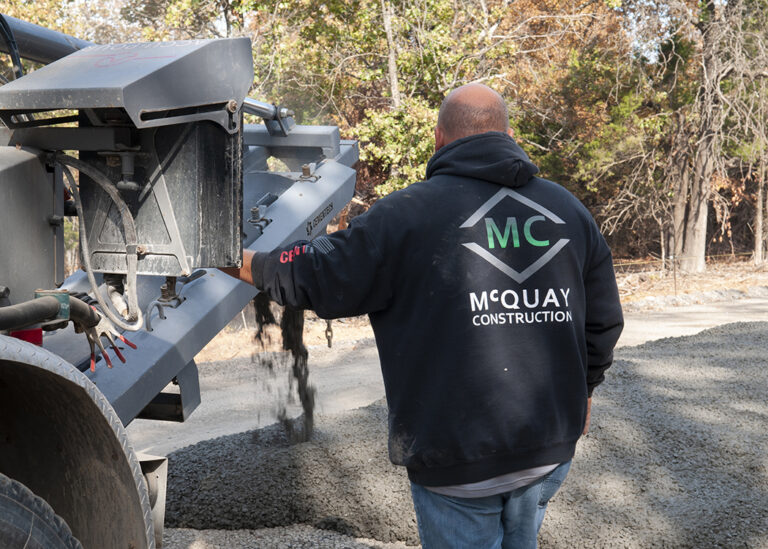
Control
The use of ACCU-POUR™ allowed McQuay to closely monitor yields and materials, ensuring accuracy in their mix design and overall project success.
"*" indicates required fields
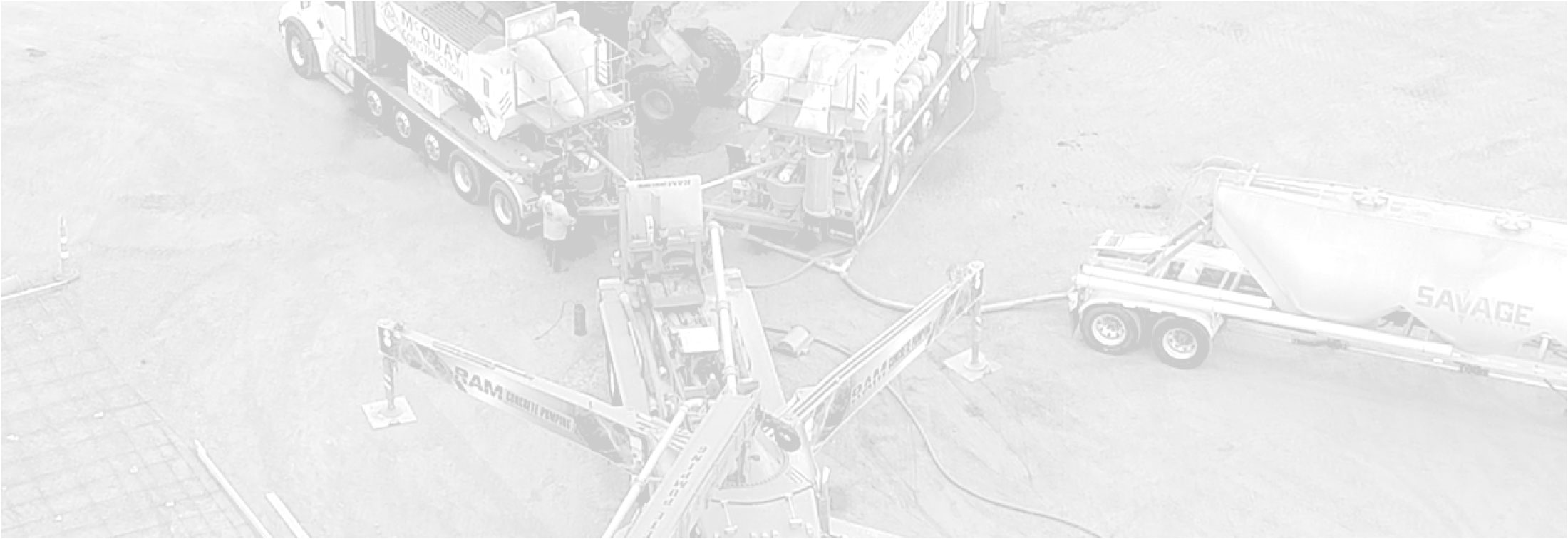