Setting up a Continuous Pour with Volumetric Concrete Mixers
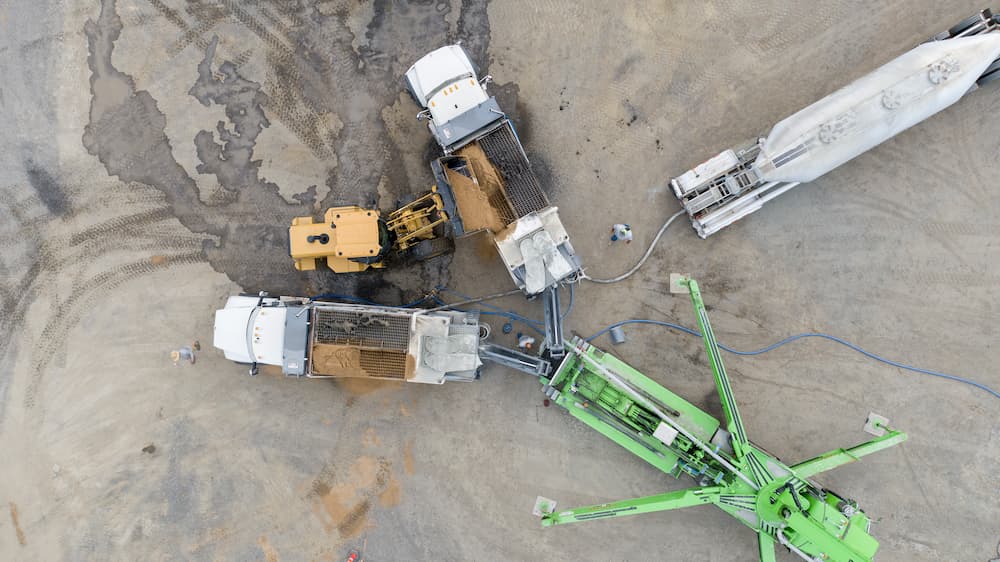
Volumetric concrete mixers excel at continuous pours, providing top-quality concrete with less equipment and fewer trucks on the road. Productivity soars as crews no longer have to wait for the next ready-mix truck. A steady stream of fresh, consistent concrete at the correct slump gives a competitive edge when quality and time management are priorities.
McQuay Construction is an industry-leader in using volumetric trucks for continuous pours. Through trial and error, the company helped perfect the process. The following five-step process helps McQuay achieve unmatched efficiency and quality.
1. Take control.
“It is much easier when you own all of the equipment,” says Zach McQuay.
McQuay Construction owns all the equipment used to produce concrete on the job site, including the concrete pump, the volumetric concrete mixers, water trucks when needed, pneumatic cement powder trailers, and wheel loaders. This simplifies scheduling since you have control of each part of the process. You do not have to schedule around the owner of the pump truck or the cement powder supplier for example.
2. Stage equipment.
The volumetric concrete mixer truck must be properly staged with the concrete pump and pneumatic cement trailer.
“To do a continuous pour, you have to dump into a concrete pump,” explains McQuay.
You first choose the area where the pump truck is going to sit. Then you need to select where to position the volumetric cement mixer trucks in relation to the pump. Each volumetric concrete mixer truck should be positioned in a Y-pattern off the corner of the pump so there is room for a loader to operate in between and load materials into the volumetric concrete mixers.
Then you need to position the pneumatic cement trailers where they can access the volumetric concrete mixers but be easily swapped out without disturbing continuous production. If a water truck is needed, it is positioned in front of or right beside the concrete pump.
3. Source the water.
Water is a critical ingredient for producing concrete. You need an ample supply for the volumetric mixer in a continuous pour application. In the best-case scenario, water can be sourced from a nearby hydrant with the hoses run to the volumetric concrete mixers. If a hydrant isn’t available on-site, you will need a water truck to shuttle water to the volumetric mixers.
Perfecting Continuous Concrete Pours
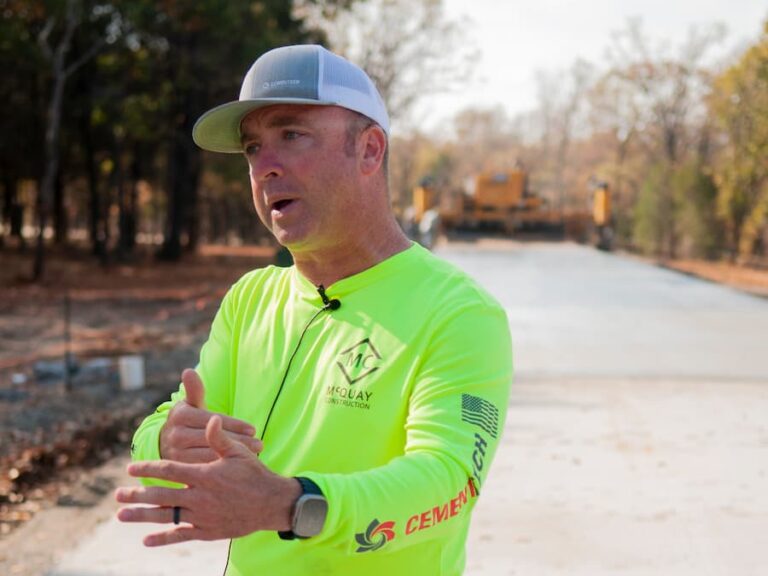
Learn how McQuay Construction uses volumetric mixers to set up and run continuous pours for quality, consistent concrete. Discover their five-step process for top results and easy operation.
4. Stage material stockpiles.
“The material placement is very important,” says McQuay.
Stockpile enough material to complete the job on site. When staging the materials, you need to plan for the appropriate spacing for the loader to maneuver and efficiently feed the volumetric mixer. Rock and sand should be placed where they can be loaded into the truck with minimal movement. McQuay stockpiles his rock on the right side and sand on the left side of the volumetric mixer trucks.
If the piles can be positioned on concrete, you can eliminate any potential loss of material.
5. Ensure cement powder availability.
McQuay consistently pours a 3500 psi mix design at 120 yd3 an hour with two volumetric trucks. This requires careful planning. Running short on any material brings the entire operation to a standstill.
“You always have to plan and schedule ahead to make sure that you have enough material to get the job done,” says McQuay. “It is very easy to stockpile enough rock and sand. Cement powder is another game. Without powder, you do not have concrete.”
Cement powder is a more limited resource that must be secured by a vendor in advance of the project. McQuay stores cement powder in silos which is transported to the site in the company’s pneumatic cement trailers. The pneumatic trailer holds enough cement powder for just over 90 yd3 of concrete.
“We constantly make sure there is enough powder for today and tomorrow. You have to make sure the silos are full and that you have backup trailers,” said McQuay.
With the equipment and materials properly staged in the quantities required, continuous concrete production can be achieved with minimal labor.
McQuay Construction is an industry-leader in using volumetric trucks for continuous pours. Through trial
and error, the company helped perfect the process. The following five-step process helps McQuay achieve
unmatched efficiency and quality.
“When set up properly, one operator can run two trucks in a continuous pour using volumetric trucks and a remote control. Once production is started it doesn’t stop,” said Zach McQuay, Owner of McQuay Construction. “The operator continually monitors the water/cement ratio.”
While it sounds complicated, McQuay Construction can lay out a continuous pour in an hour and be up and running if the rock is already there.
Proper setup yields quality results
Producing a continual flow of fresh concrete using the five steps outlined, volumetric concrete mixers eliminate the common problem of cold joints and seams.
“If the ready-mix truck needs to stop for 20 minutes while the crew catches up, you have to add another 10 gallons of water to get the concrete mix back to the right consistency. There is nothing you can do about it. With the volumetric truck, we can simply hit stop. There is fresh concrete available as soon as you are ready to go again,” said McQuay.
Adding water to the ready-mix trucks compromises concrete strength. By producing fresh concrete on demand, volumetric concrete mixers provide concrete at the ideal slump with no additional water required. The result is a quality product that maintains maximum psi strength with no consistency variation.
If the ready-mix truck needs to stop for 20 minutes while the crew catches up, you have to add another 10 gallons of water to get the concrete mix back to the right consistency. There is nothing you can do about it. With the volumetric truck, we can simply hit stop. There is fresh concrete available as soon as you are ready to go again.
"*" indicates required fields
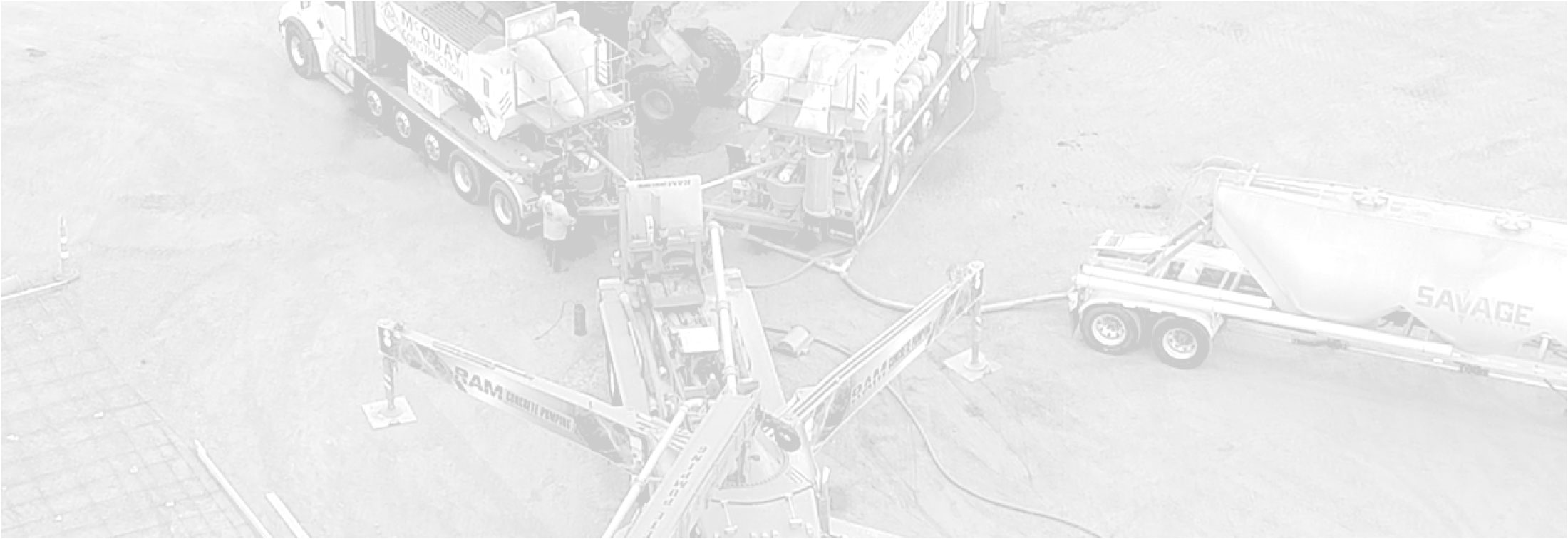