Ever wondered how mobile concrete trucks can save you time and money? Or maybe you’re curious about the latest technology in volumetric mixers? Inside Mix is where you’ll find real stories from people using these solutions every day. Dive into our case studies, see what customers are saying, and get expert tips on everything from mixing the perfect batch to finding the right equipment for your project.
Featured Article
Micro-Trenching Accelerates High-Speed Internet Installation in Neighborhoods
Global Optics works with utility providers to bring high-speed internet to neighborhoods by laying fiber optic cables using a method called micro-trenching
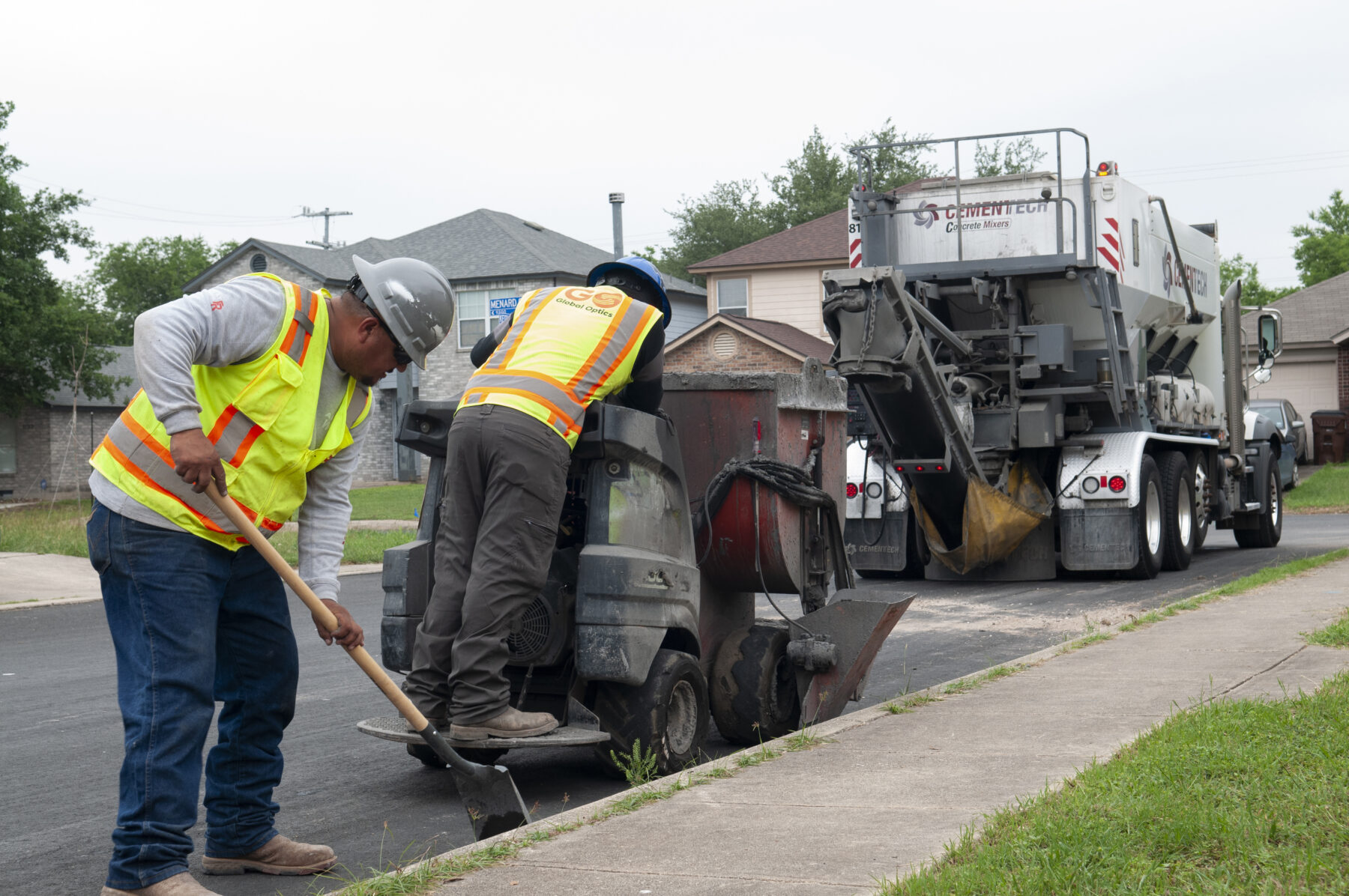
Filter Articles
Results
Subscribe to the newsletter
Want to see more?
Check out our videos
Who We Are
At Cemen Tech, we’re all about giving you control—over your concrete, your schedule, and your budget. As leaders in the industry, we design and deliver the most accurate and advanced volumetric mixers on the market. We build strong partnerships by offering innovative solutions, advanced technology, and customized options. Our employee-owned structure and core values ensure we are focused on helping your business achieve its goals.
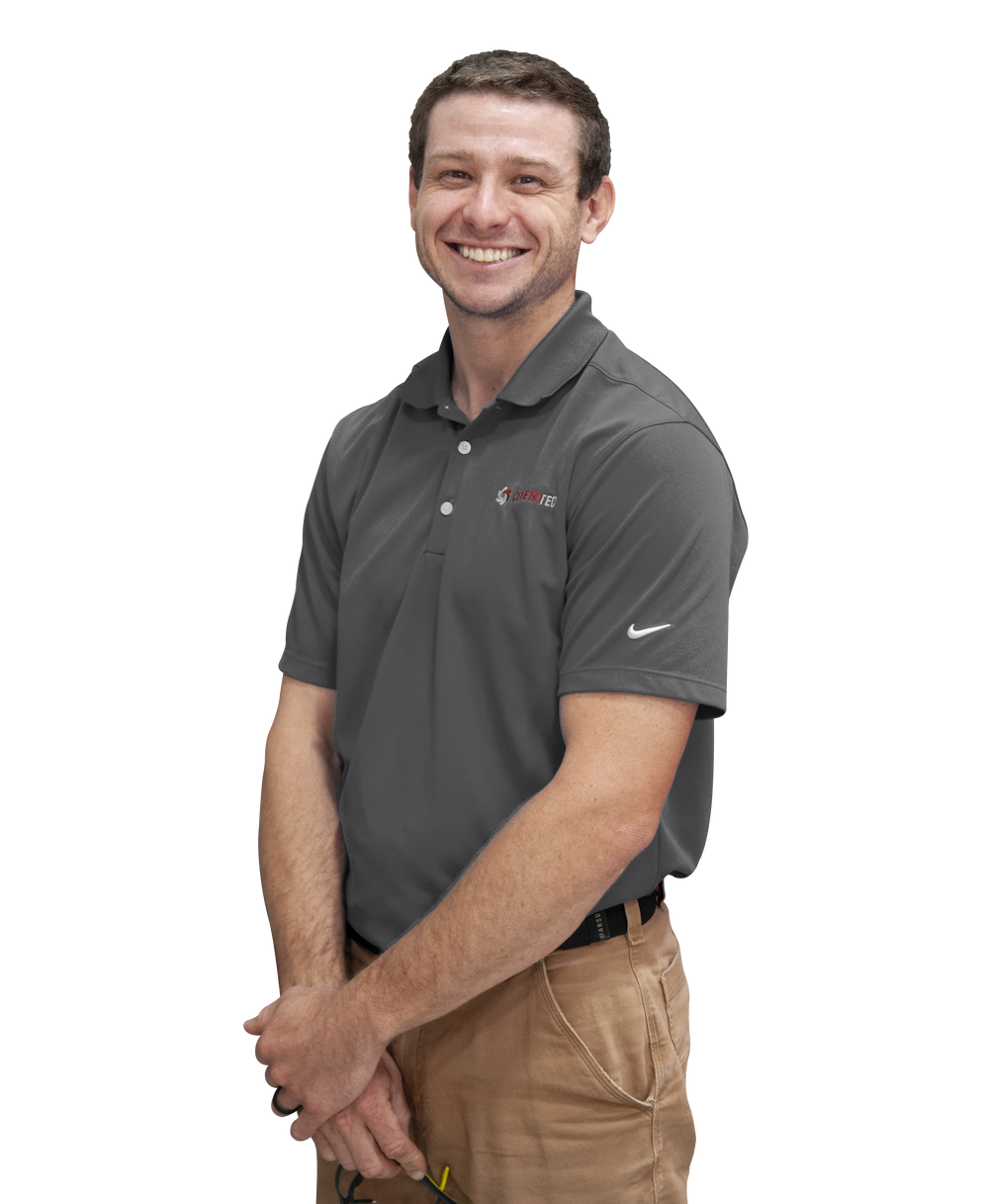
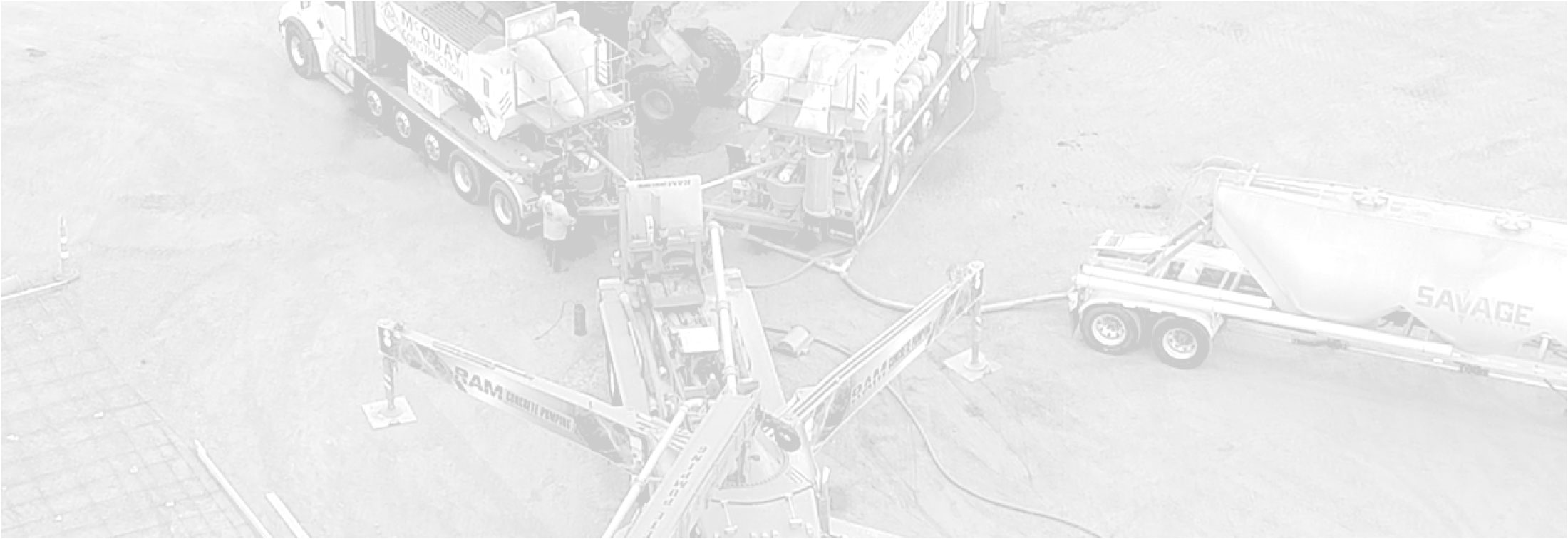